The right team for your success
We are proud to have supported many customers in making their projects a success. We successfully combine openness, creativity, interest and customer focus with expertise and the latest technical possibilities.
We have no reservations and master our projects with the spirit of Formula 1. Close cooperation with our customers is an important part of our success. Without this, it would be impossible to implement the best solutions at record speed and in premium quality.
We take an in-depth look at our customers’ products and environments and strive to think at least one step ahead of our competitors – whether this is in the development stage or in the case of established products that are being further developed.
Here we provide you with insights into several successful use cases that we have been lucky enough to be part of together with our partners and customers.
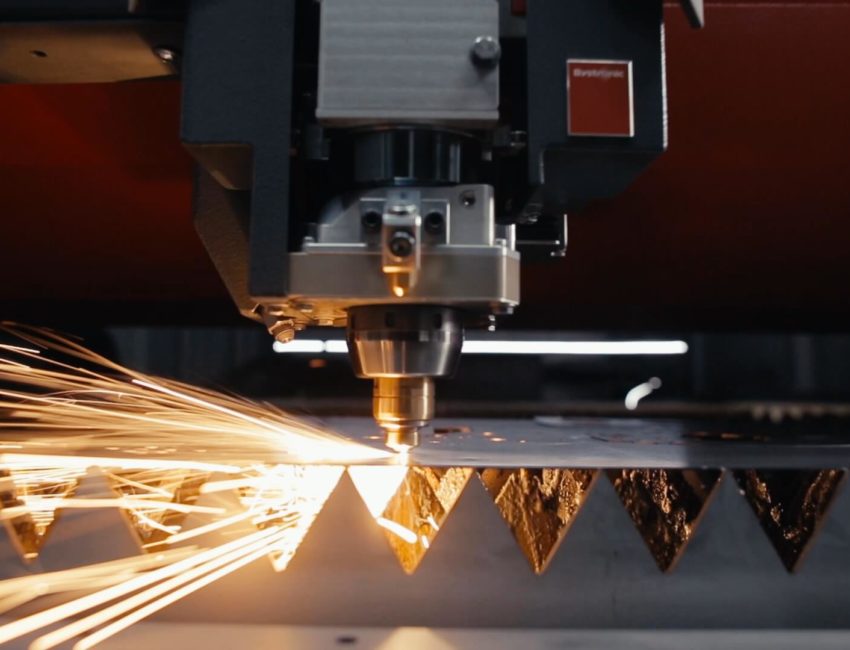
Find out more about how our services can be used.
Formula 1 technology
for sheet metal working
Lasers are used for cutting in sheet metal processing. These lasers generate enormous heat in the cutting area, which must be cooled. To ensure this cooling, we produce a stainless steel component for our customer using 3D metal printing.
To the story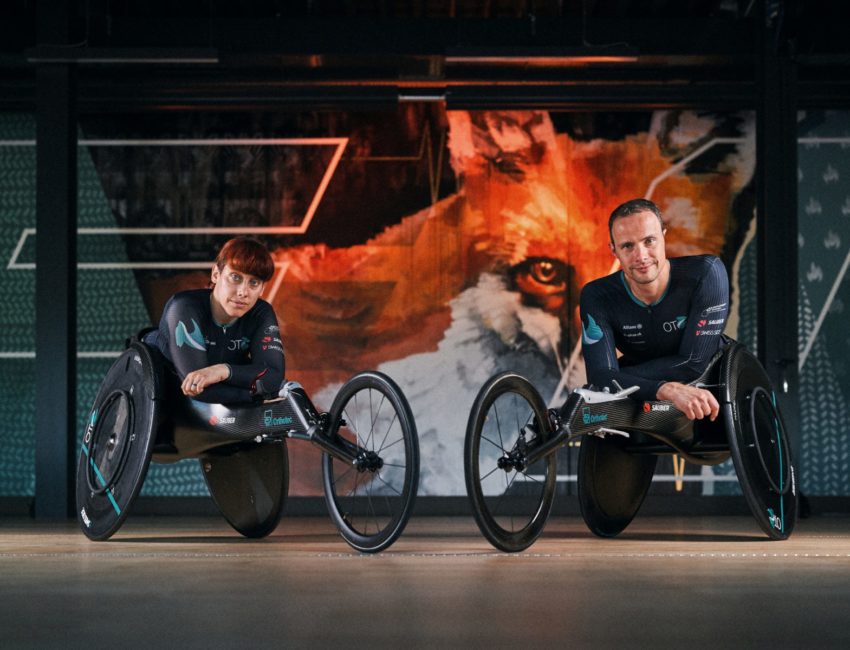
Find out more about how our services can be used.
Formula 1-technology
for wheelchair athletes
We were commissioned to develop the world’s fastest wheelchair for the Olympics in Tokyo. We used state-of-the-art CFD simulations, wind tunnel tests, 3D printing in plastic and metal as well as the latest knowledge in carbon production to build the OT FOXX M1 with which Marcel Hug won four Olympic gold medals.
To the story
Find out more about how our services can be used.
Formula 1-technology
for hydropower
The development of modern hydropower plants poses major challenges for industry. In addition to complex CFD calculations, model tests are also used. Together with our customer, we have perfectly adapted the model building process and optimised it for additive manufacturing using plastic 3D printing.
To the story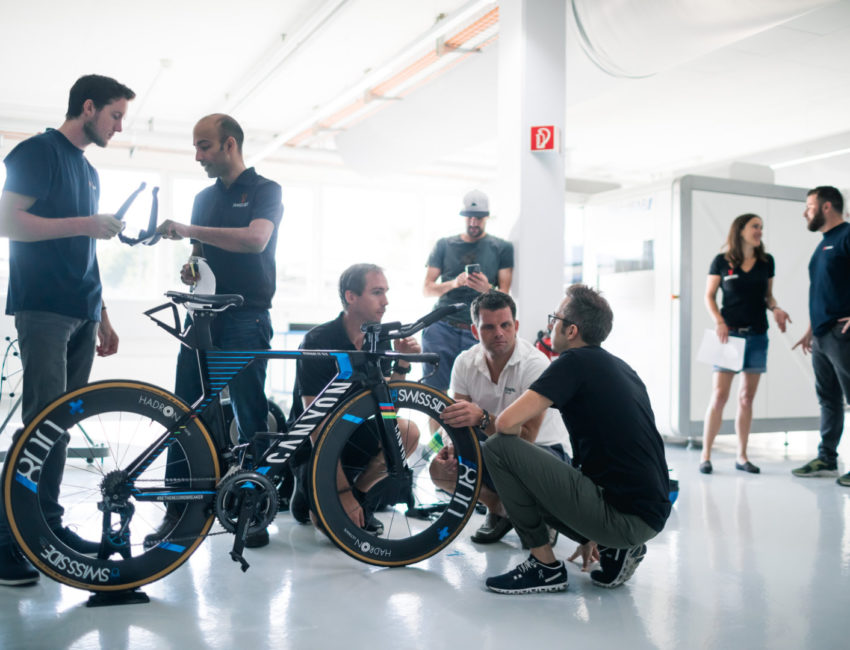
Find out more about how our services can be used.
Formula 1-Technology
for triathlon world champion
The Ironman in Kona, Hawaii, is one of the greatest challenges the sport of triathlon has to offer. Together with the bike manufacturer Canyon and our colleagues from Swiss SIDE, we have developed for Patrik Lange an aerodynamically optimized handlebar stem, a so-called aero cockpit, and produced it using additive metal manufacturing in titanium.
To the story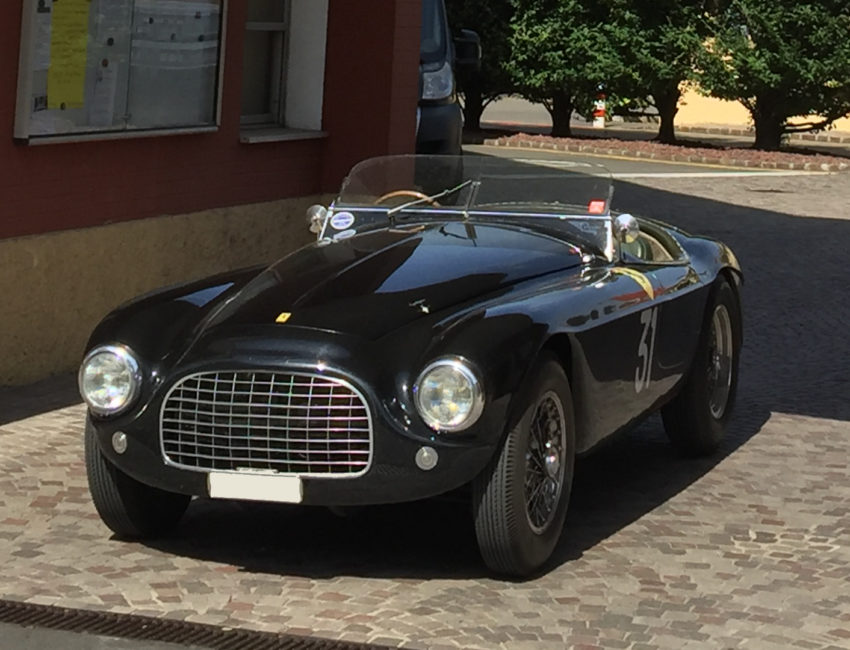
Find out more about how our services can be used.
Formula 1-technology
for legends
There are only two original Ferrari 340 America Barchetta in the world. In one of these legendary vehicles, the rear axle transmission broke. We had the pleasure of manufacturing the necessary spare part for our customer using metal 3D printing in AlSi10Mg and our internal mechanical production system, allowing the legend to take to the road and the racetrack once again.
To the story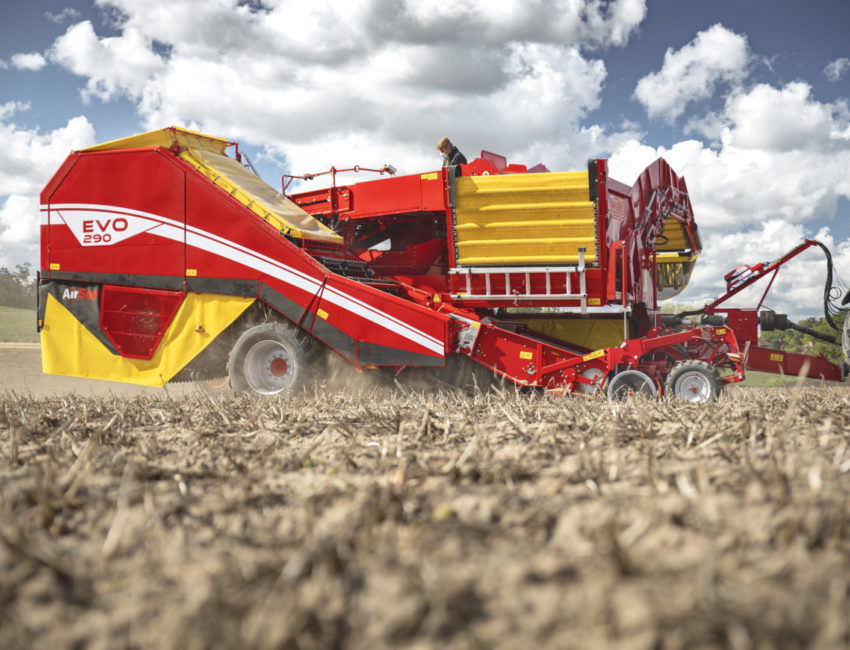
Find out more about how our services can be used.
Formula 1-technology
for potato harvest
Grimme’s Airsep system is one of the biggest innovations in potato harvesting technology. It separates the potatoes from the straw and stones while still on the harvester. Grimme contacted us with the challenge of optimizing the Airsep system.
Using CFD simulations and analyses, we significantly improved the Airsep system by making it lighter and more energy efficient.
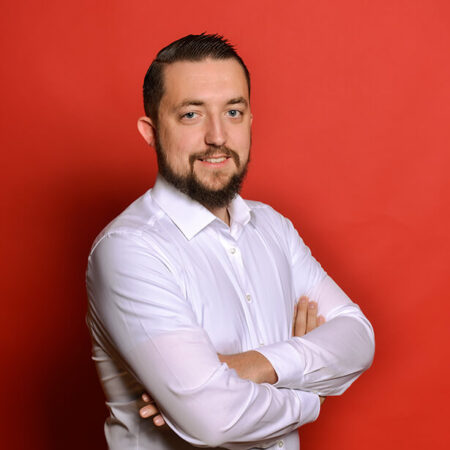
Got questions?
Leonardo MahlerDo you have any questions? Simply get in touch with me and I will be happy to advise you.