World-class 3D plastic printing
We’ve operated our own 3D plastic printing production facility for more than 20 years now. We use the best SLS and SLA materials, boast state-of-the-art facilities and employ highly motivated staff. All this, combined with the entire spectrum of post-processing possibilities, allows us to provide you and our customers with the best quality, which we too expect of ourselves.
From functional prototypes and shiny trade fair models through to serial production – we support you all the way and ensure that your 3D plastic printing project is a roaring success.
Benefits of 3D plastic printing at Sauber Technologies
Low costs
Lightweight
Maximum stability
Customised implementation
Unique industrial manufacturing
Using plastics for 3D printing is not a new idea. We’ve been producing plastic parts using 3D printing for more than 20 years now. Today, we are pursuing the clear goal of using the process on an industrial scale by using twelve large systems for SLA and SLS. We help our customers get the most out of additive manufacturing and give them the tools to manufacture parts more quickly, cost-effectively and easily. We use the same processes and techniques that are used in Formula 1 and will guide you through the entire operation, from the initial idea through to serial production.
Powder development
When it comes to producing the best parts, we rely not only on our expertise and state-of-the-art technology, but also on the very best materials. For selective laser sintering (SLS), we have managed to incorporate Formula 1 technology into 3D printing and combine the best properties of PA12 with carbon fibres. The result is HiPAC, which impresses with its outstanding mechanical properties and a wide range of possibilities for post-processing.
Our aspiration is to continue to introduce developments to keep up with changing needs. That’s why we are constantly researching materials in order to meet the growing needs. Our in-house materials laboratory and our experienced material experts are on hand to offer support.
Quality & processes
When manufacturing components, we leave nothing to chance. From the raw material through to the finished component, we monitor the entire process and are thus able to detect irregularities before they occur. The high level of process security and clear processes enable us to manufacture the best products – with unlimited reproducibility and premium quality. This has enabled us to turn additive manufacturing into a method that can be used on an industrial scale. Topics such as “production on demand” and the “digital supply chain” become tangible and applicable and are no longer a mere vision for the future.
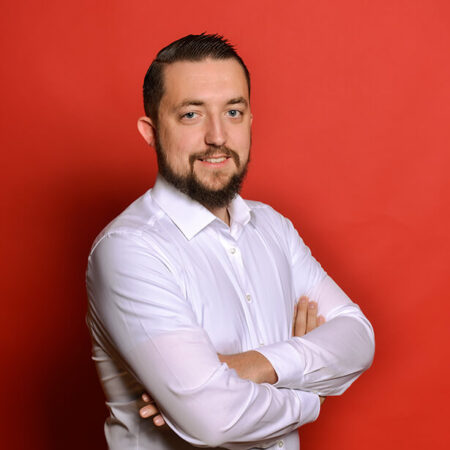
Our AM materials
- HiPAC (SLS)
- HiDEF-12 (SLS)
- HPC / PIV (SLA)
- Xtreme (SLA)
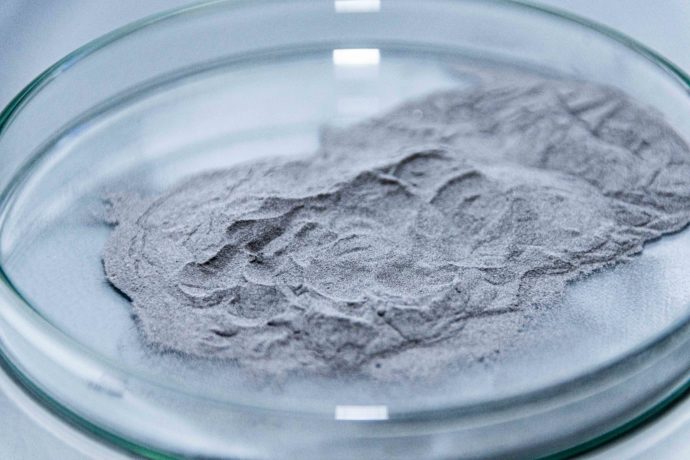
You can find further important information about our AM materials here.
Download material listPost-processing in-house
The post-processing of plastic parts is as versatile as the selection of materials. In order to achieve the ideal solution quickly and in the best quality, we rely on our wide-ranging internal expertise in:
- Manual and mechanical reworking
- Sandblasting
- Surface finishing
- Coatings
- Painting
- Modelling
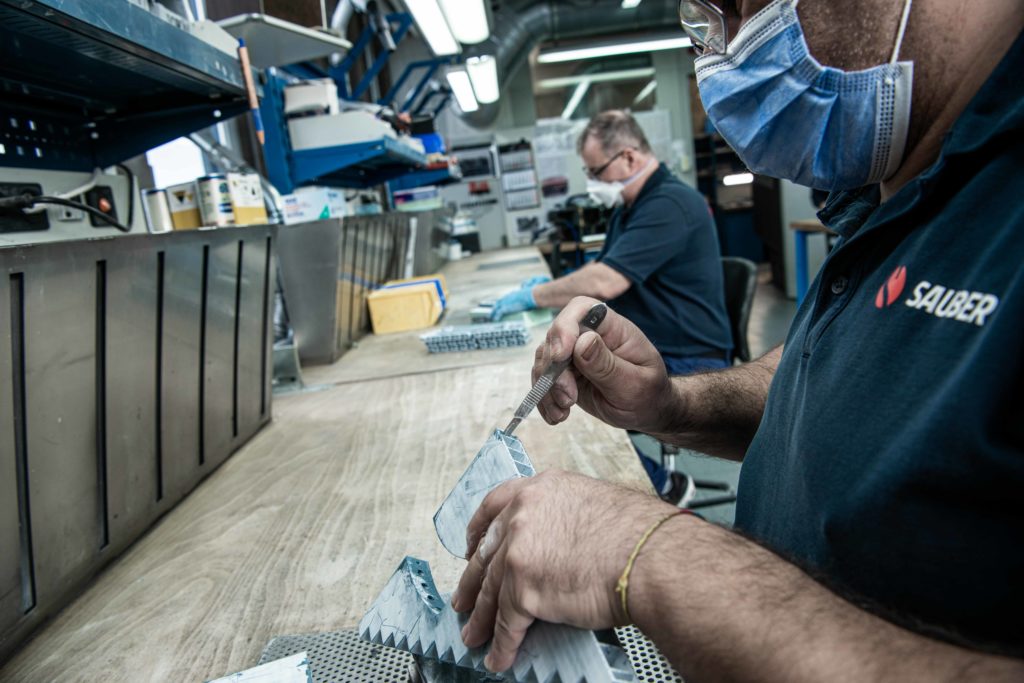
Ultramodern machinery
Win-win partnership
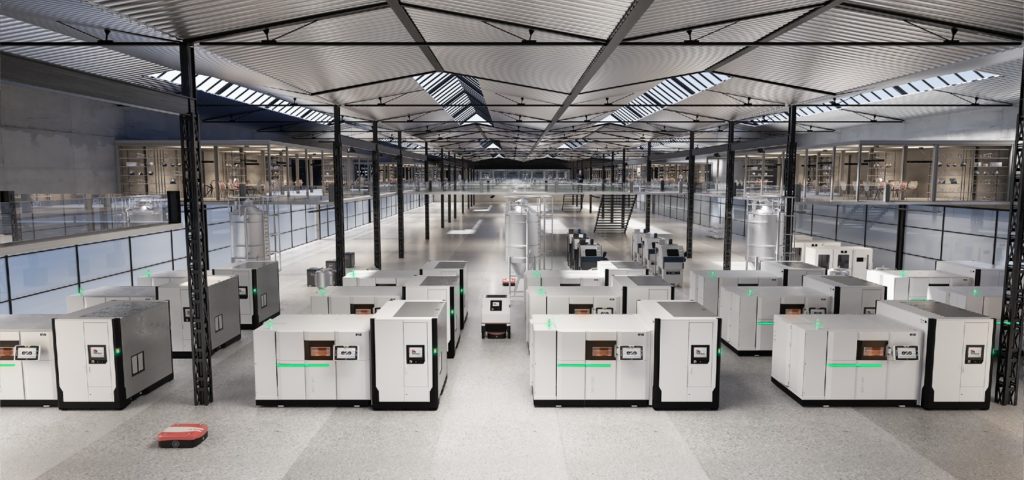
EOS Electro Optical Systems
With EOS, we have found the partner who is the global leader in industrial 3D printing. Together, we will integrate additive manufacturing of plastics into our production environment in a fully automated way. We are proud to be a pioneer in the future of production.
Rösler AM Solutions
We are proud to work closely with the best partner for the surface treatment of additively manufactured components. Rösler AM Solutions supports us not only with the best equipment, but also supports us and our customers with tailor-made solutions for the best products.
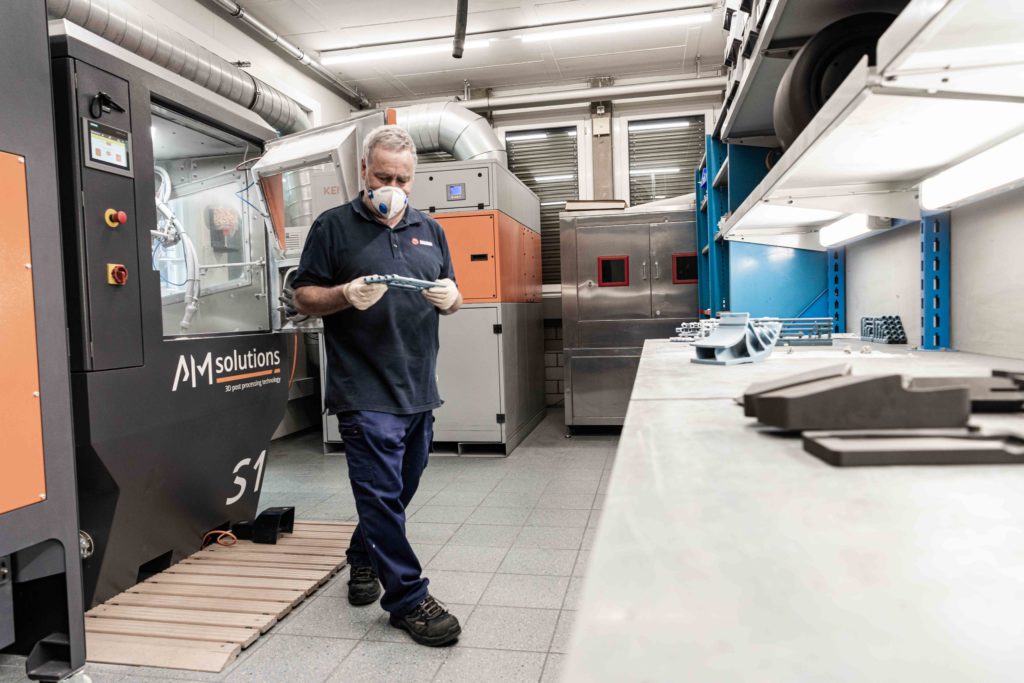
Additive success begins with engineering
We will share our expertise and many years of experience with you in order to support you with challenging projects right from the word go.
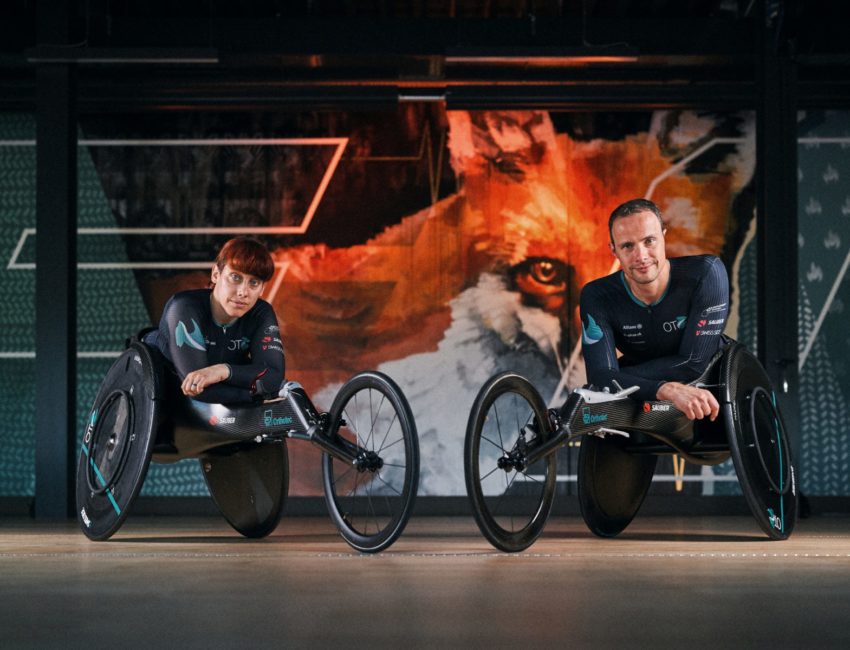
Formula 1-technology
for wheelchair athletes
We were commissioned to develop the world’s fastest wheelchair for the Olympics in Tokyo. We used state-of-the-art CFD simulations, wind tunnel tests, 3D printing in plastic and metal as well as the latest knowledge in carbon production to build the OT FOXX M1 with which Marcel Hug won four Olympic gold medals.
To the story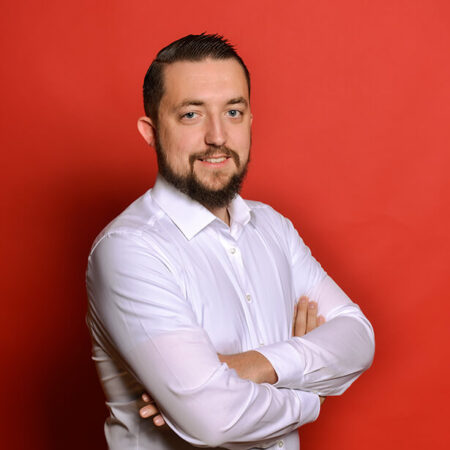
Got questions?
Leonardo MahlerDo you have any questions? Simply get in touch with me and I will be happy to advise you.